An effective warehouse management system is a critical pillar of success in today’s fast-paced world. The importance of warehouse management systems (WMS) has grown in popularity as a result of the increased demand for efficient order processing, accurate inventory control, and streamlined operations.
Intelligent software solutions have become indispensable tools for businesses in a variety of industries, assisting them in navigating the complex environment of supply chain management. In this post, we will look at why a Warehouse Management System is necessary, delve into the key features of a warehouse management system, detail best practices for implementation, and show how this software can continually optimize your operations.
Table of Contents
What is a Warehouse Management System (WMS)?
A Warehouse Management System (WMS) is a software solution that automates and optimizes warehouse operations.
It is critical in controlling and overseeing the day-to-day operations of a warehouse, including receiving, storing, picking, packing, and shipping items.
WMS is a critical tool for companies trying to improve the efficiency, accuracy, and visibility of their supply chain and inventory management.
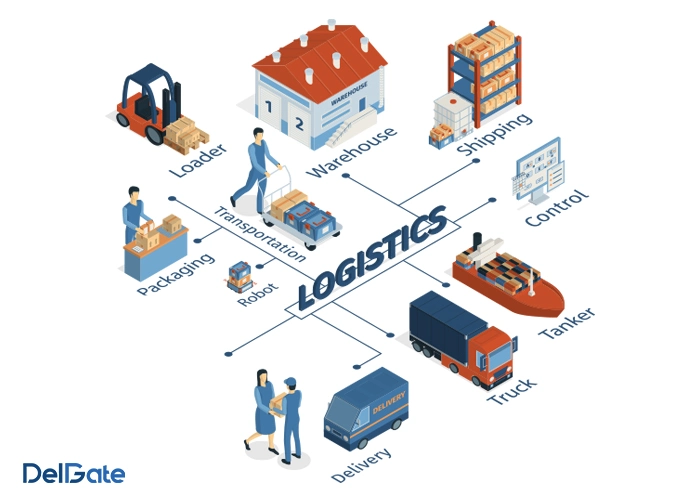
Importance of warehouse management system
The importance of a Warehouse Management System (WMS) in modern business operations cannot be overstated. As businesses face the complexities of managing diverse inventories, fulfilling customer orders efficiently, and navigating dynamic supply chains, a robust WMS becomes a crucial asset. WMS enhances operational accuracy by automating tasks, provides real-time visibility into inventory levels, and streamlines order fulfillment processes. This not only improves overall efficiency but also contributes to better customer satisfaction through timely and accurate deliveries.
Moreover, the data insights generated by a WMS empower businesses to make informed decisions, optimize warehouse space, and adapt to changing market demands. In essence, the adoption of a Warehouse Management System is a strategic investment that aligns with the evolving landscape of modern supply chain management.
The Need for a Warehouse Management System
Businesses encounter increased challenges in controlling inventory and completing orders in today’s digitally altered environment. Manual methods are no longer sufficient to meet the demands of growing operations and diversified client requests. This is where the importance of a Warehouse Management System (WMS) comes into play, especially when considering the specific needs of businesses in Vancouver, where an advanced inventory management system Vancouver is essential for navigating the intricacies of the local market.
Read more: The Importance of Warehouse Sorting Process and Sorting Facilities
A WMS provides numerous critical benefits:
- Automation: WMS automates many warehouse activities, decreasing the need for manual labor. This automation not only speeds up procedures but also reduces the possibility of errors, resulting in improved accuracy.
- Efficiency: WMS dramatically improves overall warehouse efficiency by improving the flow of items and tasks. This guarantees that products move quickly through the warehouse, avoiding bottlenecks and delays.
- Inventory Control: Because WMS provides real-time visibility into inventory levels, businesses can maintain exact stock control. This decreases the possibility of overstocking or understocking, which improves cost-effectiveness.
- Order Fulfillment: A warehouse management system (WMS) streamlines order fulfillment by assisting warehouse personnel to choose, pack, and transport items reliably and on time. This results in increased consumer satisfaction and loyalty.
- Scalability: As a company grows, WMS can easily adjust to new demands. A strong WMS can scale to handle these changes, whether it’s processing more SKUs, orders, or warehouse sites.
Key Functionalities to Evaluate
- Inventory Management: Inventory management is a critical component of WMS. inventory management system Vancouver provides a real-time view of stock levels, locations, and movement, allowing for precise stock counts and efficient tracking.
- Order Fulfillment: WMS aids in order processing by ensuring that the correct products are picked, packed, and dispatched to clients accurately and on schedule.
- Space usage: In a warehouse, efficient space usage is crucial. WMS optimizes storage sites to reduce waste and provide simple access.
- Labor Management: It aids in labor allocation and work assignment, increasing warehouse employee productivity.
- Receiving and Putaway: WMS manages the efficient intake of goods, directing them to the right storage locations based on factors like demand and item characteristics.
- Picking and Packing: WMS optimizes the picking process, suggesting the most efficient routes and methods. It also manages packing and shipping processes, ensuring compliance with customer requirements.
- Shipping and Transportation Management: It manages the shipping process by generating shipping labels, tracking shipments, and making carrier selection easier.
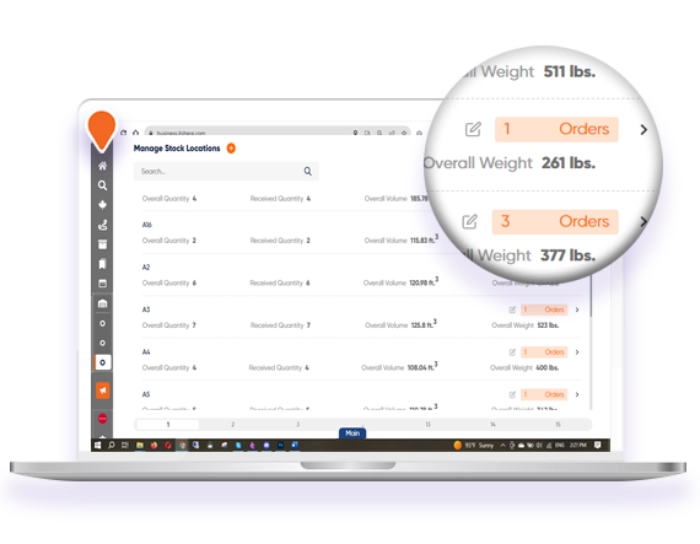
Read more: Deliver Pricey Furniture with DelGate: A Trusted Vancouver-Based Logistics Company
Best Practices for Implementation
Implementing a WMS requires careful planning and execution. Here are some best practices to ensure a successful integration:
- Assessment and Strategy: Begin by assessing your warehouse operations and identifying pain points. Develop a clear strategy that aligns the WMS implementation with your business goals.
- Engage Stakeholders: Involve key stakeholders from different departments to ensure that the chosen WMS meets the needs of various teams.
- Data Migration and Integration: Ensure smooth data migration from existing systems to the WMS. Test integrations thoroughly to prevent data discrepancies.
- Training and Change Management: Provide comprehensive training to your staff on using the new system. Address any concerns and foster a culture of adaptability.
- Phased Implementation: Roll out the WMS in phases to minimize disruption. Monitor each phase closely and make necessary adjustments before proceeding.
- Continuous Evaluation: Regularly assess the system’s performance, gather feedback from users, and make necessary refinements to optimize its functionality.
Warehouse Management Problems and Challenges:
While WMS is a powerful tool, various obstacles and issues must be addressed to ensure its successful adoption and operation:
Integration: One of the most difficult difficulties is connecting WMS with existing systems such as ERP software, inventory management system Vancouver, and e-commerce platforms. Data consistency and correctness are ensured through seamless connection.
User Adoption: Getting warehouse employees to adapt to new technologies can be difficult. Proper tutorials and support are required to ensure that personnel can effectively use the WMS.
Scalability: As a company expands, so do its warehouse requirements. WMS must be scalable to support expanded inventory, orders, and storage needs.
Data Accuracy: WMS relies on accurate data. Any discrepancies in inventory data can lead to errors in efficient order fulfillment, resulting in customer dissatisfaction and increased operational costs.
Customization: Different industries and businesses have unique warehouse processes. Customization options in WMS are crucial to adapting the system to specific requirements.
Read more: Customized Fulfillment Services: A Tailored Approach to Optimize Your Business Operations
Inventory Visibility: Achieving real-time visibility into inventory across multiple locations can be challenging. A robust WMS should provide accurate inventory tracking capabilities.
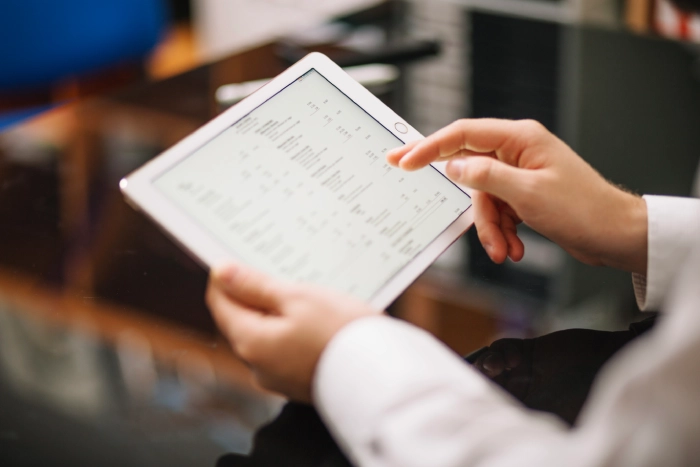
RFID and Barcode Implementation: Utilizing RFID (Radio-Frequency Identification) and barcode technologies can enhance accuracy and efficiency. However, implementing these technologies can be costly and complex.
Cost Management: The cost of implementing and maintaining a WMS can be substantial. Businesses need to carefully manage these costs to ensure a positive return on investment.
Regulatory Compliance: Depending on the industry, there may be regulatory requirements related to inventory tracking, reporting, and safety that the WMS must support.
At DelGate, we have addressed all the fundamental challenges and key aspects of WMS for our customers.
Continuous Optimization through WMS
Once implemented, a Warehouse Management System becomes a dynamic tool for continuous optimization. Benefits of warehousing management system ripple across various aspects of your operations:
- Enhanced Accuracy: The precise tracking and automated processes significantly reduce errors, leading to higher accuracy in order fulfillment and inventory management.
- Faster Order Processing: Streamlined workflows and real-time data access enable faster order picking, packing, and shipping, resulting in improved customer satisfaction.
- Resource Efficiency: Optimal allocation of labor and resources leads to increased productivity and reduced operational costs.
- Scalability: As your business grows, a WMS can accommodate increased order volumes and new warehousing challenges, ensuring scalability.
- Real-Time Insights: Access to real-time data and analytics empowers informed decision-making, enabling you to identify areas for improvement and capitalize on emerging trends.
conclusion
In conclusion, a Warehouse Management System is more than mere software; it’s a transformative force that elevates your warehouse operations to new heights. By centralizing and automating critical tasks, it empowers businesses to navigate the complex logistics landscape with agility and precision.
From inventory control and order fulfillment to labor management and integration capabilities, a well-implemented Warehouse Management System (WMS) offers a comprehensive solution to optimize your operations. Embracing this warehouse management technology solutions WMS not only improves efficiency and accuracy but also positions your business for sustained growth and success in the dynamic world of supply chain management.
What key features should I look for in a WMS for labor management?
Look for features like task assignment, performance tracking, and workload balancing to optimize labor efficiency. These elements contribute to streamlined operations and increased productivity.
Can a WMS adapt to changing inventory demands?
Yes, a WMS provides real-time visibility into inventory levels, enabling businesses to adapt quickly to changing demands, optimize stock levels, and prevent overstock or stockouts.