Logistics and supply chain management are often used interchangeably, but there are significant differences between the two. Understanding these differences is essential for businesses to optimize their operations and achieve success. In this blog post, we will explore the various perspectives that distinguish logistics and supply chain management and how they impact businesses. We will also delve into the differences between logistics, supply chain, and value chain and provide examples of how they impact a business.
What are the Four Different Perspectives which Distinguish Logistics and Supply Chain Management?
To understand the differences between logistics and supply chain management, we must first explore the four perspectives that distinguish them. The four perspectives are: the focus of attention, scope of activities, time frame, and organizational boundaries.
The focus of attention in logistics is on the movement of goods from one place to another, while supply chain management focuses on the coordination of activities across the entire supply chain. The scope of activities in logistics is limited to transportation, warehousing, and inventory management, while supply chain management encompasses a broader range of activities, including procurement, production, and distribution. The time frame in logistics is short-term and operational, while supply chain management takes a long-term and strategic approach. Finally, the organizational boundaries in logistics are limited to a single company, while supply chain management involves the coordination of multiple companies.
Examples of How the Four Perspectives Impact Logistics and Supply Chain Management:
To better understand how the four perspectives impact logistics and supply chain management, let’s look at some examples. For instance, if a logistics manager is focused solely on the transportation of goods, they may not consider the impact of inventory levels on customer service. On the other hand, a supply chain manager would take a broader view and consider how inventory levels, production schedules, and transportation impact customer service.
In terms of scope, a logistics manager may focus solely on managing a warehouse, while a supply chain manager would look at the entire supply chain, from raw materials to finished products. In terms of time frame, a logistics manager may be focused on meeting immediate shipping deadlines, while a supply chain manager would take a longer-term approach, looking at the overall efficiency and effectiveness of the supply chain.
Finally, when it comes to organizational boundaries, a logistics manager may only be responsible for managing their company’s transportation and warehousing, while a supply chain manager may need to coordinate with multiple companies, including suppliers, manufacturers, and distributors.
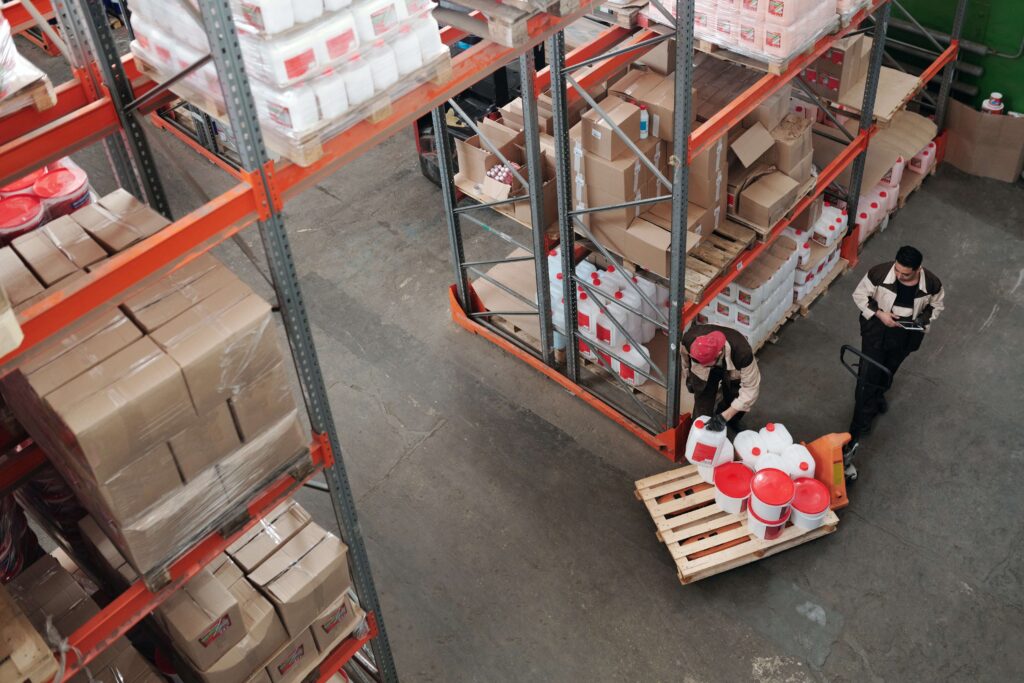
Table of Contents
How is Logistics Different from Supply Chain vs Value Chain?
While logistics and supply chain management are often used interchangeably, they are distinct concepts. To understand the differences, it’s important to first define each concept. Logistics refers to the process of planning, implementing, and controlling the movement of goods from one place to another, including transportation, warehousing, and inventory management. Supply chain management, on the other hand, involves the coordination of activities across the entire supply chain, including procurement, production, and distribution. The value chain refers to the entire set of activities involved in creating, delivering, and supporting a product or service, including marketing and customer service.
The key difference between logistics and supply chain management is the scope of activities involved. Logistics is focused solely on the movement of goods, while supply chain management encompasses a broader range of activities. Additionally, the value chain takes an even broader view, encompassing all activities involved in creating and delivering a product or service.
Examples of How Logistics, Supply Chain, and Value Chain Impact a Business:
Logistics, supply chain, and value chain all play important roles in the success of a business. For instance, a business that focuses solely on logistics may be able to move goods quickly and efficiently, but if they don’t consider the broader supply chain, they may not be able to meet customer demands. Similarly, a business that focuses solely on the supply chain may be able to optimize their sourcing and production processes, but if they don’t consider the logistics of getting the finished products to customers, they may miss out on sales opportunities. Finally, a business that focuses solely on the value chain may be able to create high-quality products, but if they don’t consider the logistics and supply chain, they may not be able to deliver those products to customers in a timely and cost-effective manner.
In practice, these three concepts are often interrelated and impact each other in significant ways. For example, a business may need to consider both logistics and supply chain when deciding where to locate their warehouses and distribution centers. By strategically placing these facilities closer to customers or key transportation hubs, the business can reduce transportation costs and lead times. Similarly, a business may need to consider the value chain when deciding on the quality of the raw materials they use. By selecting higher quality materials, the business can create a higher-quality finished product that can command a premium price in the market.
What are the different logistics and supply chain categories?
Logistics and supply chain management are complex fields, each with their own set of categories. Understanding the various categories can help businesses create better strategies to optimize their operations.
Logistics categories include inbound logistics, outbound logistics, and reverse logistics. Inbound logistics refer to the movement of goods and materials from suppliers to manufacturers, while outbound logistics refer to the movement of finished goods from manufacturers to customers. Reverse logistics, on the other hand, involves the process of returning or disposing of products and materials.
Supply chain categories include planning, sourcing, making, delivering, and returning. Planning involves forecasting demand and creating a strategy for meeting that demand. Sourcing involves identifying and selecting suppliers, while making involves the actual manufacturing process. Delivering refers to the transportation of goods and materials to customers, while returning involves the process of handling returns and exchanges.
What are the 5 main functions of supply chain management?
Supply chain management involves the coordination and management of all activities involved in the production and delivery of goods and services. The five main functions of supply chain management are planning, sourcing, making, delivering, and returning.
Planning involves forecasting demand and creating a strategy for meeting that demand. This includes developing production schedules, setting inventory levels, and identifying suppliers. Sourcing involves identifying and selecting suppliers, negotiating contracts, and managing supplier relationships. Making involves the actual manufacturing process, including the procurement of materials and the management of production processes.
Delivering refers to the transportation of goods and materials to customers. This includes managing logistics and transportation operations, as well as customer service and order fulfillment. Finally, returning involves the process of handling returns and exchanges, as well as managing warranties and repairs.
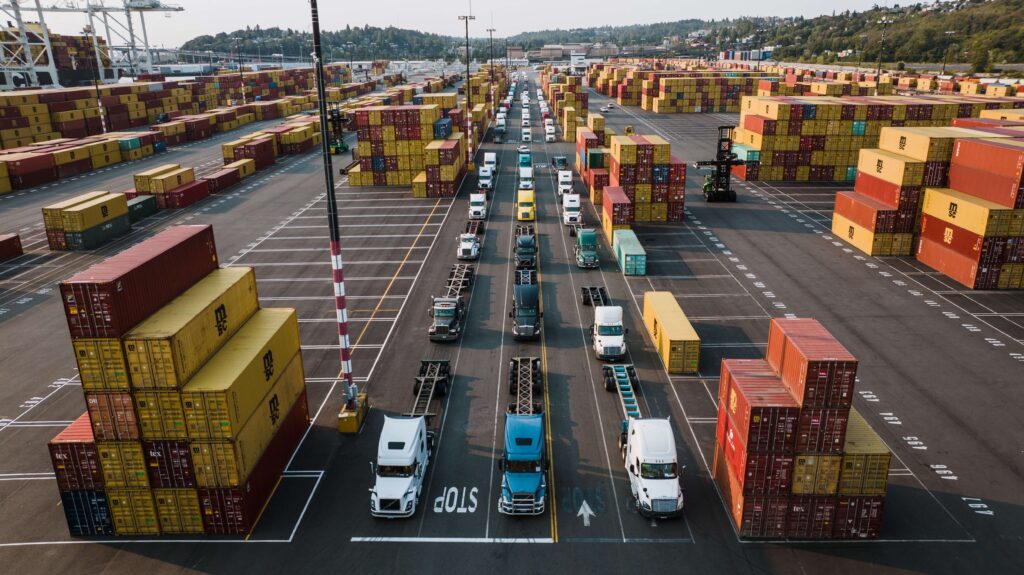
What is the advantage of logistics and supply chain?
The advantages of logistics and supply chain management are numerous. By effectively managing logistics and supply chain operations, businesses can improve efficiency, reduce costs, and enhance customer satisfaction.
Effective logistics and supply chain management can help businesses optimize their operations, reduce waste, and improve productivity. By managing inventory levels, businesses can reduce the risk of stockouts and overstocking, and ensure that they have the right products at the right time. This can also help reduce costs by minimizing the need for excess inventory storage and handling.
Logistics and supply chain management can also improve customer satisfaction by ensuring that products are delivered on time and in good condition. Effective supply chain management can help businesses improve product quality, reduce lead times, and increase responsiveness to customer needs.
Why choose supply chain and logistics?
Supply chain and logistics management are crucial for businesses to stay competitive and meet customer expectations. By having an efficient and effective supply chain and logistics strategy, businesses can streamline their operations, reduce costs, and improve customer satisfaction.
A. Explanation of why a business should choose supply chain and logistics
Choosing the right supply chain and logistics strategy can have a significant impact on a business’s success. By optimizing the movement of goods from raw materials to finished products, businesses can reduce lead times, improve inventory management, and minimize costs. Additionally, a well-designed supply chain and logistics strategy can help businesses mitigate risks, such as supply disruptions and product recalls.
B. Examples of how choosing supply chain and logistics impact a business
For example, a company that manufactures electronic goods may choose to implement a just-in-time (JIT) supply chain strategy. By only ordering and receiving raw materials when they are needed for production, the company can reduce inventory holding costs and minimize waste. Similarly, a company that sells perishable goods may choose to implement a cold chain logistics strategy to ensure that products are transported and stored at the correct temperature to maintain quality.
C. Importance of choosing the right supply chain and logistics strategy
It is important for businesses to choose the right supply chain and logistics strategy that aligns with their unique business goals and objectives. This may involve conducting a supply chain and logistics analysis to identify areas for improvement and opportunities for optimization.
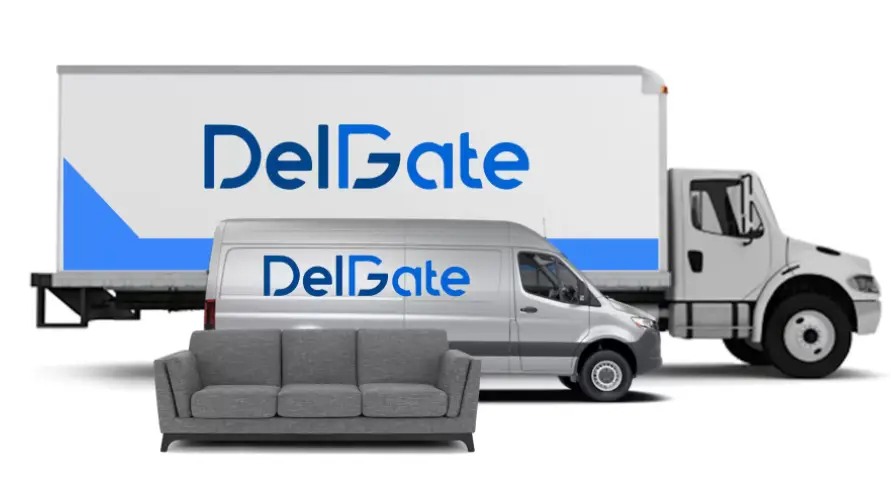
Conclusion
In conclusion, understanding the difference between logistics and supply chain management is essential for businesses to optimize their operations and stay competitive. By implementing an effective supply chain and logistics strategy, businesses can improve efficiency, reduce costs, and enhance customer satisfaction. We encourage readers to take the time to evaluate their own supply chain and logistics processes and consider implementing changes to improve their overall performance.
Learn more about our services here.